Application of thermal spray coatings
The use of technologies of gas-thermal methods of spraying and surfacing will reduce and eliminate the influence of such factors as high temperature, corrosion, erosion, cavitation, friction on the wear of parts due to the application of wear-resistant, corrosion-resistant, erosion-resistant, anti-friction, heat-resistant and other coatings.
Our technologies will improve reliability, reduce the cost of manufacturing parts and maintenance, and extend the service life.
Wear resistant coatings
Depending on the operating conditions of the parts, we offer coatings operating under the conditions of liquid lubricant, under dry friction, at elevated temperatures, under erosion dust wear, etc.
We will help you protect your details from:
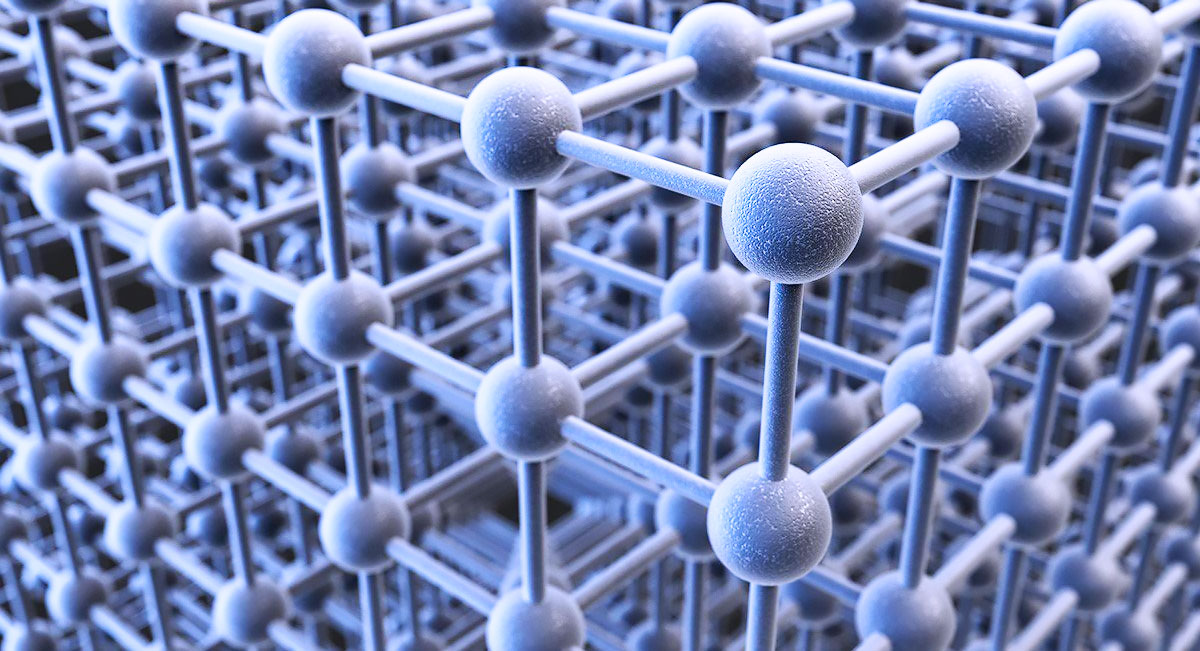
- corrosive wear
- gas abrasive wear
- hydroabrasive wear
- cavitation wear
- mechanical wear
- fretting wear
- abrasive wear
Corrosion resistant coatings
Corrosion-resistant coatings - gas-thermal metal coatings that can withstand the external effects of aggressive media.
A thin layer of metal with other properties is sprayed onto the surface of the metal structure or product, which corrodes much more slowly, protecting the main material of the part.
Metal anticorrosive coatings are applied to the metal surface for corrosion protection, hardness, electrical conductivity, wear resistance and decorative purposes.
We will help you protect your details from:
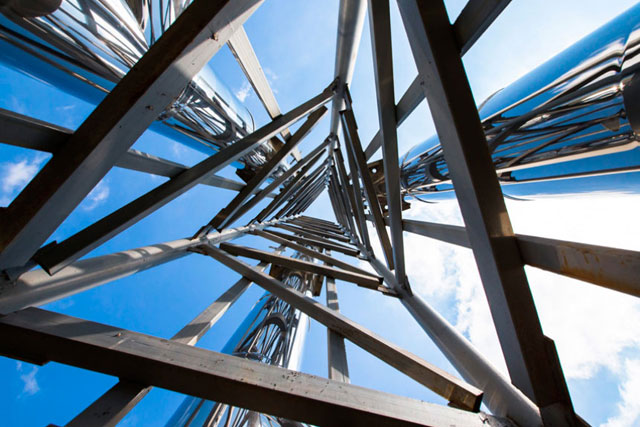
- atmospheric corrosion
- crevice corrosion
- fretting corrosion
- marine corrosion
- electrochemical corrosion
- chemical corrosion
- gas corrosion
- biocorrosion
- коррозии под напряжением
Thermal barrier coatings
Thermal barrier coatings are a system of coatings used to isolate the base material of parts operating at elevated temperatures from its impact.
Heat shielding coatings are used to reduce heat transfer. They have low thermal conductivity and maintain a large temperature gradient when exposed to heat flux.
- thermal barrier coatings
- heat-resistant coatings
Electrically conductive coatings
They are used to protect against corrosion large metal structures (bridges, supports, fences), aluminum and steel products (application of copper tracks, strips, contact pads), ceramic products.
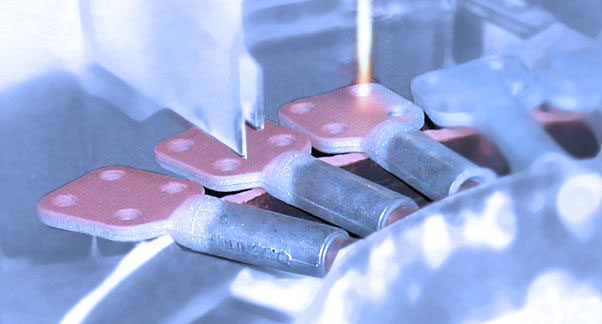
Insulating coating
Electrically insulating coatings withstand heating to very high temperatures, protecting the base material from corrosion and wear, such as, for example, ceramic coatings.
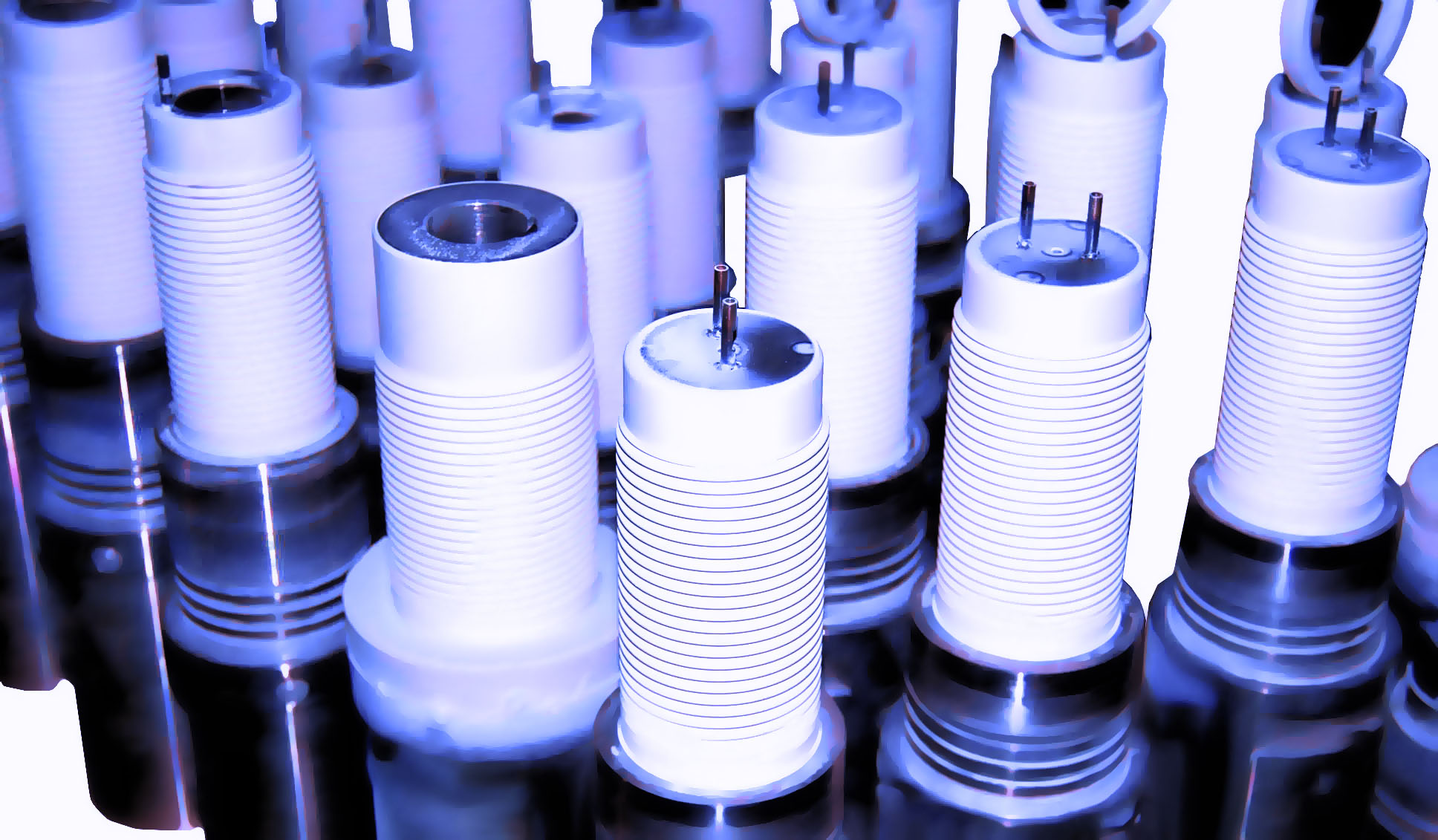
Sealing coatings
Seals are divided into:
- seals for fixed joints,
- sealing of movable joints.
By reducing the clearance between the blades and the engine casing of the turbine, an increase in its efficiency can be achieved. One way to achieve this is to apply sealing coatings to the inner surface of the stator parts, which form a minimum gap as a result of wear when interacting with the blades of the rotating rotor.
The use of sealing coatings in the turbine at the same time can solve the problem of protection against the effects of high temperatures reaching 1200ºC
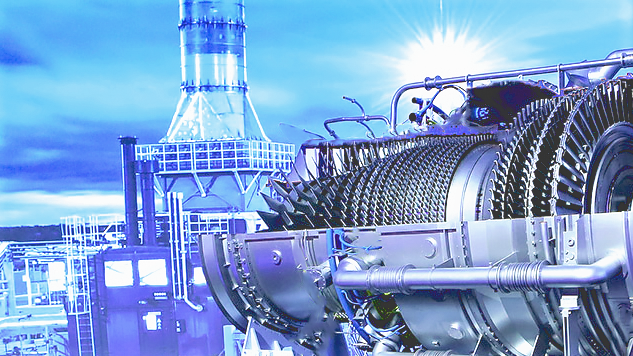