Высокоскоростное напыление карбида вольфрама и другие газотермические методы для ремонта валов, роторов, плунжеров, штоков, рабочих колёс, лопастей, корпусов, подшипников скольжения; запорной арматуры в промышленности.
Проблемы модернизации основных фондов предприятий, качественного ремонта, продления ресурса оборудования напрямую связаны с вопросами эффективности и безопасности производства. В связи с высоким износом технологического оборудования, например в энергетической, химической и нефтегазовой отраслях промышленности остро стоит вопрос его эффективного ремонта, обеспечивающего восстановление работоспособности, повышение надёжности, продления сроков эксплуатации при снижении затрат на ремонтно-восстановительные работы.
Проведенный анализ показывает, что при использовании современных технологий реально в течение длительного периода поддерживать оборудование в работоспособном состоянии без замены его на новое. Это позволяет на ~30% снизить затраты на капитальный ремонт (как показывает опыт отечественных и зарубежных предприятий), увеличить межремонтный пробег оборудования, а также обеспечить достаточный запас времени для технического перевооружения предприятий.
Метод газотермического нанесения покрытий, разработанный и реализуемый предприятием «Технологические системы защитных покрытий», уже показал свою эффективность в аэрокосмической и оборонной отраслях промышленности и вполне доступен для освоения и другими отраслями, использующими технологическое и машинное оборудование с повышенными требованиями к его надёжности и безопасной эксплуатации.
На основе структурного анализа компоновки и функционального назначения технологических установок можно выделить основные детали и узлы эксплуатируемого оборудования, для которых при ремонте эффективно использование газотермических методов нанесения защитных покрытий. В газовой, нефтяной и нефтехимической промышленностях − насосно-компрессорное и турбинное оборудование: посадочные места роторов; лопатки и диски паровых, газовых турбин и компрессоров; уплотнительные поверхности на роторе и статоре; подшипники скольжения; посадочные места подшипников и уплотнительных поверхностей статора; рабочие поверхности колёс и лопастей; штоки и плунжеры; элементы торцевых уплотнений; трубопроводная арматура: уплотнительные поверхности клиновых, шаровых и шиберных задвижек; уплотнительные поверхности приводных элементов; поверхности гидро- и пневмоприводов; электродвигатели: роторы; посадочные места корпусных элементов (рис 1);
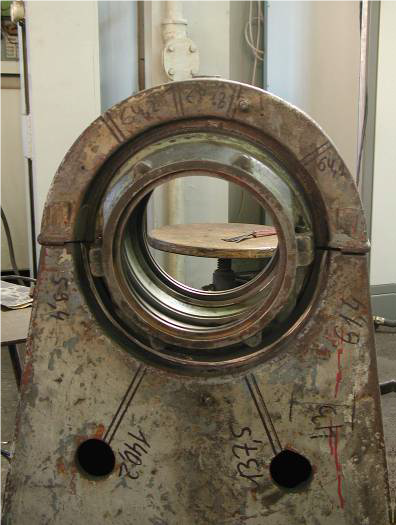
Рис. 1. а) Процесс восстановления посадочного места вала; б) Корпус опорного подшипника после проведения ремонта.
Так, например, ремонт корпуса опорного подшипника и посадочных мест под подшипники якоря электродвигателя мощностью 1350 кВт проведенный методом газопламенного напыления позволил при небольших затратах полностью восстановить ресурс дорогостоящих шаровых опор. ёмкостное оборудование: защита от коррозионного и эрозионного износа внутренних и наружных поверхностей реакторов, колонн, аппаратов, резервуаров; узлы и детали оборудования для производства полимерных материалов: шнеки; фильеры; ножи экструдеров; подшипники скольжения в резинотехнической промышленности; каландры; вальцы; смесители. В энергетической промышленности − насосно-компрессорное оборудование: валы, роторы, плунжеры, штоки, рабочие колёса, лопасти, корпусные детали, подшипники скольжения; 3 запорная арматура: уплотнительные поверхности шаровых, шиберных, клиновых задвижек, элементы приводов запорной арматуры, штоки паровой арматуры высокого давления и др. (рис. 2); теплообменное оборудование: ремонт и упрочнение (защита от коррозии и эрозии) поверхностей теплообменников, подвергающихся коррозии и золовой эрозии; детали паровых и газовых турбин: посадочные места шеек роторов, посадка дисков, защита от газо-абразивной эрозии лопаток, баббитовые подшипники, защита и восстановление лопаток газовых турбин; дымососы, роторы и лопасти; валы электродвигателей; посадочные места в чугунных корпусных элементах; защита от коррозии металлоконструкций и др.; защита от коррозионного и эрозионного изнашивания корпусного оборудования.
Приведенный перечень не в полной мере охватывает всю гамму оборудования, где возможно использование методов газотермического напыления, но только перечисленные выше узлы и детали составляют около 60- 70% изнашиваемых элементов, которые определяют ресурс работы изделий, их производительность, и по стоимости составляют до 30% закупаемых комплектующих (большей частью импортных) изделий. Реальное освоение современной техники и технологии газотермический покрытий может и должно комбинироваться с внедрением других современных технологических решений, например, передовых методов сварки, сборки, испытаний, контроля состояния оборудования и прогнозирования его ресурса, обеспечивая комплексные подходы к решению задач не только повышения фондоотдачи, но и надёжности и безопасности эксплуатации оборудования.
Некоторые из применяемых технологий широко известны не только в России, но и за рубежом, другие являются новыми, разработанными и запатентованными у нас в стране. Внедрение газопламенного напыления взамен наплавки, например, при восстановлении посадочных мест под муфты, шестерни, зубчатые колеса и т.п. позволяет избежать термических поводок деталей и структурных изменений в материале основы из-за отсутствия нагрева деталей.
Для восстановления регулирующих органов запорной арматуры ООО «ТСЗП» был использован высокоскоростной метод напыления. Это дало возможность при небольших затратах в два раза увеличить срок работы штоков. Рис. 2. Штоки запорной арматуры после высокоскоростного газопламенного напыления. Для защиты деталей ГТУ (пламенных труб, рабочих лопаток) как на этапе изготовления, так и при ремонте специалистами ООО «ТСЗП» 4 предлагается метод плазменного напыления материала ZrO2-Y2O3 (рис. 3). Он позволяет намного повысить время эксплуатации газотурбинной установки. Рис. 3. Нанесение керамического теплозащитного покрытия ZrO2-Y2O3, на рабочие лопатки ГТУ. Внедрение передовых технологий обеспечивает и повышение конкурентоспособности оборудования на основе прямого использования требований стандартов передовых зарубежных стран. Безусловно, следует принимать во внимание и то обстоятельство, что внедрение современных технологий требует и повышения квалификации персонала и общей культуры производства, и определённого переоснащения машиностроительных и ремонтных производств.
Но в конечном итоге, как подтверждает отечественный и зарубежный опыт, внедрение современных технологий способствует решению двух важных задач.
1. При ремонте – обеспечить безопасную и надёжную работу оборудования при минимальных удельных затратах.
2. В машиностроительном комплексе – выпускать продукцию, соответствующую мировому уровню, что обеспечит её конкурентноспособность как на отечественном, так и на зарубежном рынках.
Учитывая реальное состояние и перспективы развития промышленности, только современные технологии могут обеспечить экономически устойчивое, ресурсосберегающее и безопасное функционирование предприятий.