АНТИКОРРОЗИОННЫЕ ГАЗОТЕРМИЧЕСКИЕ ПОКРЫТИЯ. Доклад
Газотермическое напыление металлических покрытий — это расплавление и нанесение металла на подложку. Как применяемые методы нанесения, так и сами металлы, могут быть разными, главное, что в результате на поверхности остается тонкое, более устойчивое к коррозии и эрозии, чем основной металл, покрытие.
Многолетний опыт применения металлических покрытий и тестирование с применением внешнего воздействия на поверхность доказывают, что данный метод является более эффективным в длительной антикоррозионной защите стали, чем защита краской или полимерными композициями.
Покрытия ТСЗП являются также прекрасной антикоррозийной основой под краску. Органические покрытия, нанесённые на поверхности железа и стали, портятся под действием подпленочной коррозии, которая происходит под покрытием в результате недостаточной адгезии. Тонкий слой покрытия предотвращает коррозию основания и крепко связывает сталь с органическим покрытием.
Существует много условий коррозии, таких как: природа веществ, тип коррозии, скоростной фактор и используемые металлы. Иногда их незначительные изменения становятся важным фактором в решении проблем коррозии.
Технологии
Газопламенное напыление представляет собой нагрев, плавление, диспергирование расплава и перенос расплавленных частиц материала с помощью ацетилено-кислородного пламени на металлическую поверхность детали, где формируется стабильное непрерывное покрытие.
Назначение:
- восстановление посадочных мест деталей;
- восстановление геометрии рабочих поверхностей высоконагруженных деталей;
- защита от коррозии нанесением покрытий из цинка, алюминия, нержавеющей стали и их сплавов;
- ремонт баббитового слоя подшипника;
- создание декоративного покрытия напылением латуни, меди, бронзы и других материалов.
Сущность способа электродуговой металлизации заключается в нанесении покрытий путем расплавления частиц двух расходных электродных проволок, между которыми возникает горение электрической дуги, расплавленные частицы переносятся сжатым воздухом на поверхность детали (подложку).
Назначение:- защита от коррозии нанесением покрытий из цинка, алюминия, нержавеющей стали и их сплавов;
- защита деталей от износа;
- создание декоративного покрытия напылением латуни, меди, бронзы и других материалов.
Преимущества:
- мобильность оборудования, что позволяет наносить покрытие непосредственно в процессе эксплуатации объекта или без демонтажа оборудования;
- оборудование достаточно простое в эксплуатации, не требует сложного ухода и дорогостоящего технического обслуживания;
- высокая производительность процесса и низкие эксплуатационные расходы, что позволяет наносить покрытия на крупногабаритные объекты и большие площади;
- эффективная защита от коррозии металлических конструкций; антикоррозионные покрытия, получаемые методом электродуговой металлизации, обладают протекторным свойством;
- не требуется использование кислорода, керосина или горючего газа, что уменьшает стоимость покрытия;
- может использоваться в ручном, либо в автоматизированном режиме.
Метод высокоскоростного газопламенного напыления основан на использовании в качестве источника нагрева и сообщения кинетической энергии металлическому порошку с помощью высокоскоростной газовой струи, образованной в результате сгорания топлива в среде окислителя.
Назначение:
- защита от коррозии и износа;
- нанесение твердосплавных износостойких покрытий на основе карбида вольфрама;
- нанесение жаростойких покрытий.
Преимущества:
- высокая скорость напыляемых частиц, благодаря чему получаемые покрытия обладают высокой плотностью и высокой прочностью сцепления;
- процесс происходит при относительно малом тепловом воздействии на основу;
- экологический чистый процесс, используется как замена гальванического хромирования;
- нанесение покрытия с минимальными припусками для последующей механической обработки;
- обеспечение высокой производительности и повторяемости характеристик процесса за счет автоматизации работ.
Цель создания HVOF-метода заключалась в сочетании непрерывного процесса, характерного для газопламенного метода, со сравнительно высоким качеством покрытия, как при детонационном напылении.
Преимущества HVOF-метода
• получение покрытия с минимальной пористостью (<1%) в сочетании с высокой прочностью сцепления с основным материалом (80 МПа и более);
• благодаря низкой шероховатости напыленной поверхности практически отпадает необходимость в ее последующей механической обработке (или она
требуется в минимальном объеме);
• термическое воздействие на деталь минимально по сравнению с плазменным методом напыления;
Тестирование и мировые исследования
Тестирование ЦНИИПСК имени Мельникова напыляемых металлических покрытий на устойчивость к внешнему воздействию, показало, что они имеют более длительный срок службы, чем покрытия, полученные во время окраски, которая предполагает соответствующую подготовку стального изделия и выполнение соответствующих процедур во время применения. Во многих случаях напылённый алюминий можно оставлять незащищённым, без использования пропиток.
Использование сплава алюминия с 5% магнием является прекрасной альтернативой покрытию краской. Данный сплав является эффективным покрытием для морских платформ и деталей, которые находятся на палубе корабля.
Термически напыляемый алюминий хорошо использовать для заводского оборудования, работающего при высоких температу
рах. При использовании эпоксидной пропитки, данное покрытие выдерживает до 5000 градусов С, при использовании силиконовых пропиток — более высокую температуру. В отличие от покрытия поверхности краской, изделия с покрытием ТСЗП можно использовать почти сразу же после проведения работ. Ещё меньше повреждений во время эксплуатации будет, если наносить покрытие на отдельные детали в процессе производства, что позволяет напылять покрытие на любую часть изделия, и даёт возможность осуществить сборку изделия после завершения работ или после проведения ремонтных работ.
Исследование процесса коррозии Американским Сварочным Обществом в течение 19 лет
В 1974 г. Американское Сварочное общество завершило 19-летнее изучение антикоррозийной защиты, напыляя цинковые и алюминиевые покрытия на сталь с низким содержанием углерода.
Результаты данного исследования следующие:
- Алюминиевые покрытия толщиной 0.08-0.15 мм, как с применением пропиток, так и без, обеспечивают полную антикоррозийную защиту металла-основы в течение 19 лет в морской воде и в жёсткой морской и промышленной атмосфере;
- Цинковое покрытие без использования пропитки должно быть 0.30 мм толщиной для того, чтобы обеспечить полную защиту поверхности в морской воде в течение 19 лет. В жёсткой морской и промышленной атмосфере, покрытие цинка толщиной 0.23 мм без использования пропитки и 0.08-0..15 мм с использованием пропитки, обеспечивают антикоррозийную защиту в течение 19 лет;
- Использование пропиток с алюминием улучшает внешний вид, как при этом на металле-основе не появляется ржавчины в течение 19 лет.
- Тонкий слой газотермически напылённого алюминия является более эффективным, оно имеет меньшую тенденцию к образованию вздутий, и, следовательно, имеет более долгий срок службы;
- В тех случаях, когда после использования алюминиевого покрытия возникают физические повреждения, такие как царапины, коррозия не прогрессирует, это означает, что обеспечивается протекторная защита.
Средняя продолжительность срока службы покрытия и опыт применения ТСЗП
Средняя продолжительность срока службы металлических конструкций и поддержания их эстетичного внешнего вида зависит в значительной мере от подготовки поверхности и эксплуатационных характеристик покрытия, которое будет контактировать непосредственно со сталью. В этой связи цинк и алюминий играют фундаментальную роль, не только благодаря их способности противостоять агрессивному воздействию окружающей среды, но также благодаря активному защитному действию, которую они оказывают на сталь.
Срок службы термически напыляемого покрытия против органического.
- Напыление металла — 25 лет;
- Однослойное покрытие — 15 лет;
- Двухслойное покрытие — 10 лет;
- Олифа — 5 лет.
Опыт применения
Метод напыления металлов применяется уже более 50 лет для напыления мостов, дымовых труб и деталей, более 20 лет для напыления прибрежных конструкций. В Северном море первым сооружением, которое было покрыто металлическим напылением, стало специализированное оборудование морских платформ, такое как балки сигнального факела, мостиковые перекрытия между платформами и запасные ступеньки, которое невозможно было безопасн
о заменять.
Применение газотермического напыления (основы и пропитки) требует большего количества времени, чем процесс нанесения 4 слоёв краски при использовании эквивалентных ресурсов. Причина в том, что напыляемый металл дольше наносится на поверхность, руководители стройки должны принимать это во внимание и добавлять в свои графики дополнительное время.
Дизайн металлоконструкций должен быть таким, чтобы обеспечить свободный доступ к ним металлизационого пистолета и производить напыление под правильным углом и близко к поверхности. На такие детали, как, например, верхние поверхности нижних балок на двутавровой балке, которая поддерживает палубные втулки, закреплённые на консоли плиты, и бимсовый полосовой металл очень трудно, практически невозможно термически напылять.
Автоматизация процесса помогает уменьшить усталость оператора и уменьшает возможную опасность, которую данный процесс представляет для здоровья и безопасности, а также обеспечивает напыление ровного, экономного слоя металла. Хотя, процесс автоматизации не применим для напыления сосудов сложной формы и сборных стальных рам.
Опыт применения протекторных газотермических покрытий на морских обьектах
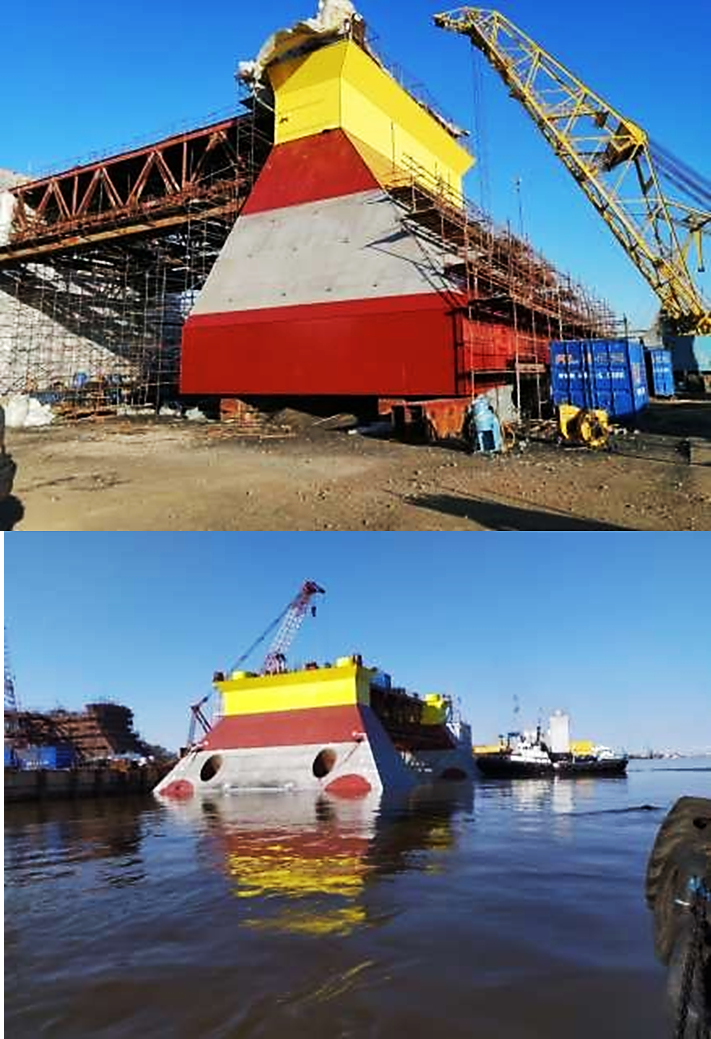
Коррозия металла – одна из ключевых проблем, возникающих во время эксплуатации морских сооружений и судов.
Морской коррозии подвергаются: металлическая обивка днищ судов, подводные трубопроводы, нефтяные платформы, различные металлоконструкции, находящиеся в воде, металлические конструкции в портах, опоры мостов и др. Основные потери обусловлены преждевременным выходом из строя металлоконструкций, стоимость которых значительно превышает стоимость металла, использованного на их изготовление. Более половины всех конструкций гидротехнических сооружений имеют металлическое основание, вследствие чего подвержены воздействию морской коррозии.
Морская коррозия по своему механизму является электрохимической. Общее высокое содержание диссоциированных солей делает морскую воду электролитом с хорошей электропроводностью.
Обледенение – еще одна актуальная проблема, возникающая во время эксплуатации морских судов и сооружений.
Антикоррозионная защита морских нефтегазопромысловых сооружений рассчитывается с учетом экстремальных погодных условий, воздействия морской воды, действия ультрафиолетового излучения, возможных механических повреждений и скопления живых существ на корпусе. При этом системы защиты от коррозии не должны оказывать негативного влияния на окружающую среду. Долговечная защита от коррозии может быть осуществлена только в случае грамотного выбора систем антикоррозионной защиты и соблюдения технологии их нанесения.
Использование эффективных средств противокоррозионной защиты и компетентный подход на всех этапах работ при их нанесении позволяют увеличить эксплуатационный период нефтегазопромысловых сооружений.